
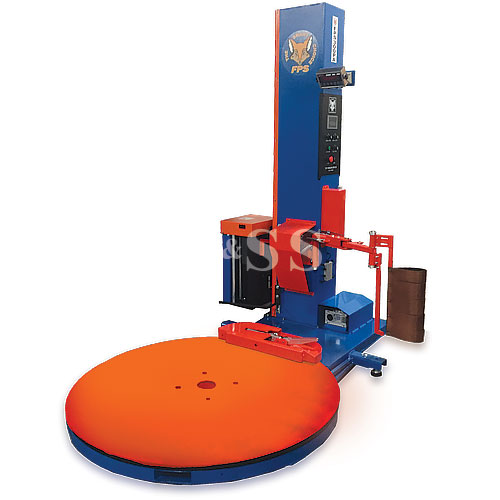
That way, a warehouse business would have to buy additional racking components from the original manufacturer. The theory was that each racking system maker would hold proprietary patents on their systems through creative slot designs. This led to manufacturing competition and many unique vertical member slot designs showing up on the market. As post-war production for civilian interests expanded, so did the demand for pallet racking components. This made rack uprights, beams and decks incompatible with one another.įollowing the war, the demand for warehousing and efficient racking didn’t slow down. Different companies produced rack systems, leading to non-uniformity in design. This dates back to World War II when massive manufacturing of war goods required pallets and related material handling equipment, including racking and shelving systems. There are clear reasons why selective racking manufacturers offer two main slot designs. Why Are There Different Racking Slot Designs? Teardrops also have parallel perforations in most applications. As their name suggests, double slots have two vertical holes sitting side by side.
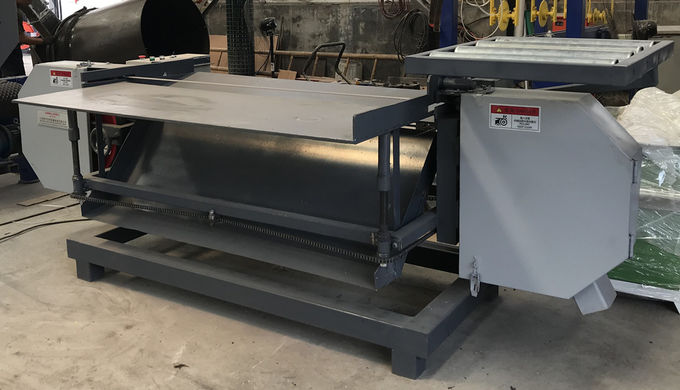
Double slots, on the other hand, are vertical incisions in the metal members.
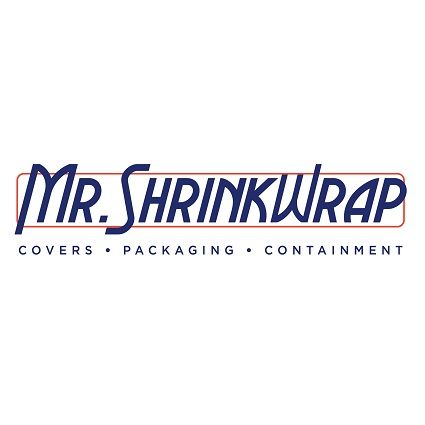
Teardrop rack connections are pear-shaped. Although there are many slot designs, there are two primary profiles commonly found within warehouses - teardrop pallet racks and double slotted pallet racks.īoth configurations get their name from their connection opening shape. Racking has evolved over the years, and the main difference is in the beam connection slots built into the racking system’s vertical or upright members. They capitalize on space, safely store a multitude of products and make workers’ jobs easy for retrieving materials and merchandise.īut, not all racks have common designs. Racks, as they’re commonly called, are indispensable pieces of material handling equipment. Most American warehouses have at least one thing in common - the need for selective pallet racking.
